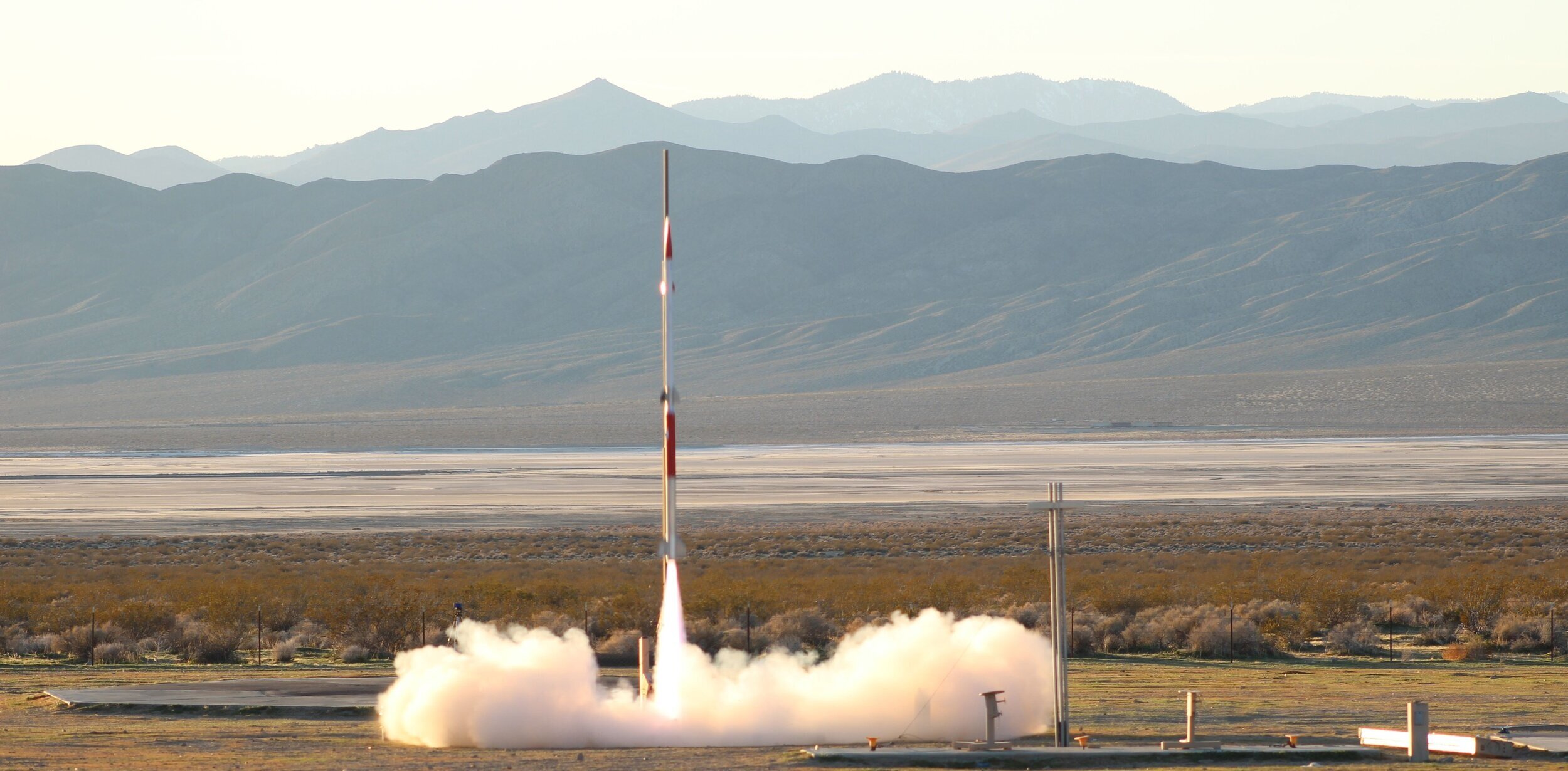
Meet the Subteams.
Rocket team requires work from a diversity of disciplines:
Propulsion
The solid propulsion subteam designs, manufactures, and tests the flight motors for our rockets. The team mixes custom ammonium perchlorate composite propellant in our lab, with formulas characterized through a series of small test fires. The team then performs system design using a simulation software developed by one of our team members. Following the full motor simulation, we design and manufacture motor hardware and cast our flight propellant grains. We static fire test all of our motor designs prior to flight to ensure consistency with our simulations. The team has successfully flown custom motors ranging in size up to a P9100.
Aerodynamics
The aerodynamics subteam is responsible for the design, manufacturing, and testing of our composites structures to include the fin can of the launch vehicle. The strength of the fin can is essential to a stable flight and a successful launch. To ensure this strength, we lay up and cure our carbon fiber laminates in-house. Our nose cones are manufactured from filament wound fiberglass and precision machined steel to endure strain during flight. Together, the fin can and nose cone protect mission-vital components until they can be secured by recovery.
Structures
The structures subteam designs and manufactures various structural components of the rocket, as well as the avionics tower. Parts like aluminum bulkheads are manufactured on CNC mills and lathes, while parts such as enclosures and panels for the avionics tower are manufactured on 3D printers and waterjets. Our components interact with all other subteams’ assemblies, making sure the whole rocket works. Structures also designs, manufactures, and tests parachutes as well as deployment hardware for each rocket. Our custom recovery system includes hand-sewn parachutes and a high-altitude pyrotechnic separation mechanism.
Avionics
The avionics subteam designs and assembles custom electronics and are currently in the process of designing a space-ready flight computer. Supporting hardware includes power management with support for on-the-pad charging and cameras, capable of recording video in Ultra HD (4K). Our multi-threaded flight software performs high-frequency sensor fusion and reports supersonic telemetry using our custom radio hardware. During the launch, we are in charge of mission control.
Liquid Propulsion
The liquid propulsion team designs, manufactures, and tests liquid rocket engines. In addition to engine development, the team manufactures all test infrastructure and feed systems required for testing. All components are manufactured on campus by team members. The team has completed fabrication of a 1.6 kN heat sink Ethanol/LOX engine ready for hot-fire, and is currently working on the design of a Kerosene/LOX regeneratively cooled engine.
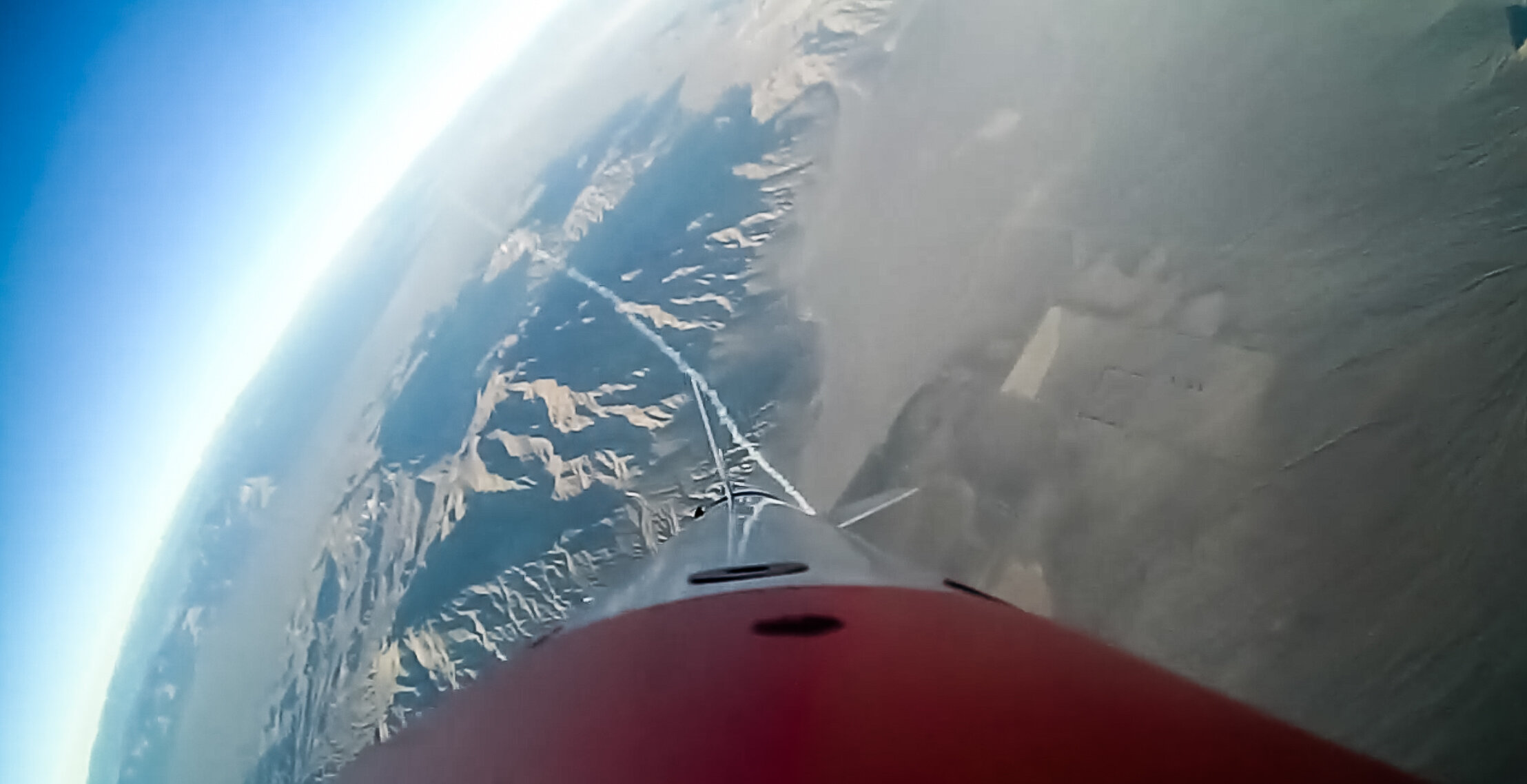